Why is DuraGrit better than my regular steel grit?
Simply put the main advantage of DuraGrit compared to cast steel grits is it lasts longer. Steel grit is a consumable product and the less you consume the less money you spend. If you consume large amounts of steel grit even a small percentage reduction can save you a lot of money. DuraGrit lasts up to 30% longer than traditional cast steel grits, the savings from this can be huge. DuraGrit is also a fast cutting abrasive. Conventional cast steel grit is manufactured by crushing cast steel shots into a grit form. Cast steel shot starts off round shaped and containing internal fractures. When crushed the resulting particles still contain some portion of the round outer shell and internal cracks. These flaws slow down the cutting speed of the grit. DuraGrit is crushed from forged high carbon chromium bearing steel. This stock material contains no internal cracks and is fully angular shaped.Abrasive Comparison Chart
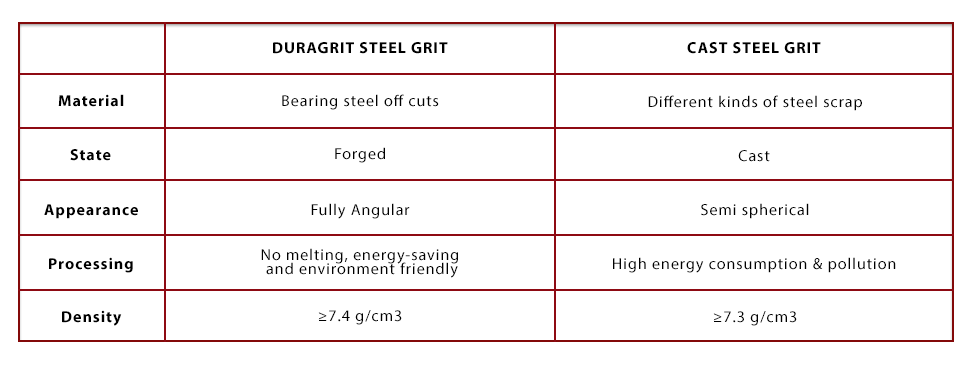
How is DuraGrit made?
The life of steel grit is largely determined by the stock steel used to produce it. DuraGrit is manufactured from forged steel offcuts used in the manufacture of bearings. Bearings are made of high carbon chromium steels. One of the factors that determine the life of bearing steel is the purity or cleanliness of steel. During the production of bearing steel the impurities are removed through vacuum degassing and consumable electrode vacuum melting. These processes produce the very pure steel stock required for bearing manufacturing. Bearing steel also contains 0.6-1.6% chromium as an alloying element. This alloy increases hardenability, improves abrasion-resistance and promotes carburization. Of the common alloying elements chromium is surpassed only by carbon, manganese and molybdenum in its effect on hardenability. Chromium forms the most stable carbide of any of the more common alloying elements, giving high-carbon chromium steels exceptional wear-resistance.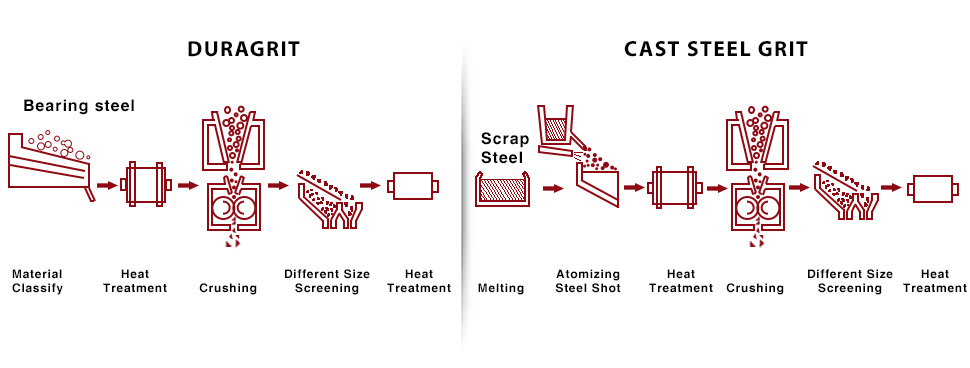
Chemical Composition and Physical Characteristics
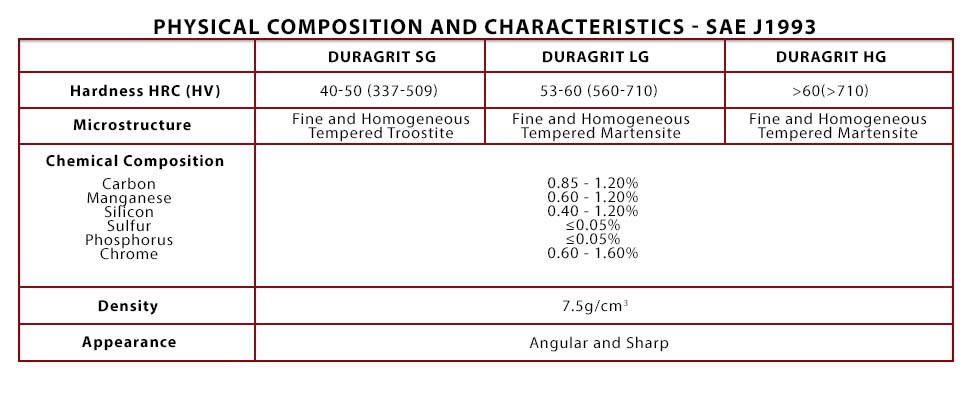
Size Distribution Chart
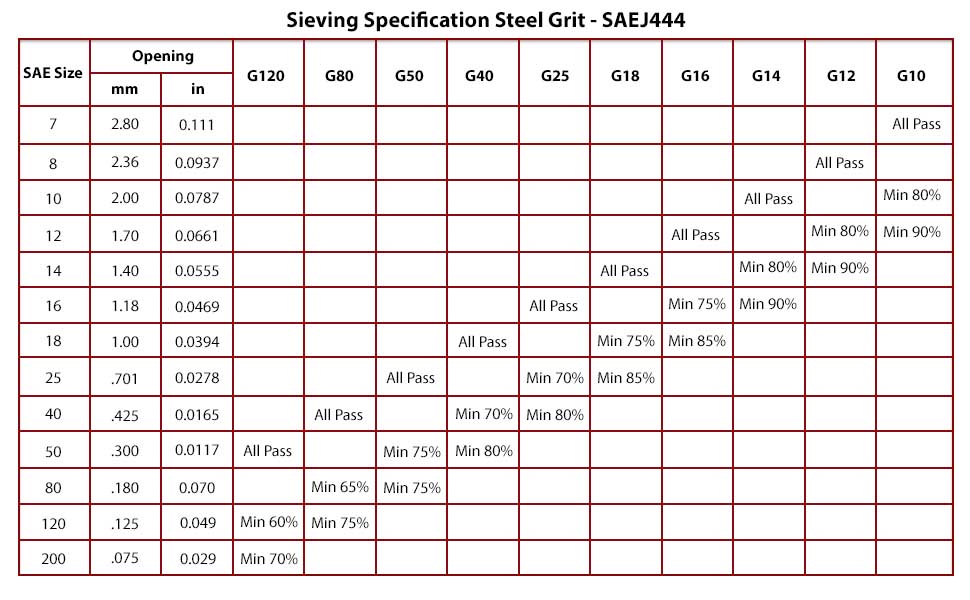
Packing
DuraGrit is available in 1 tonne pallets of 25kg bags and 1 tonne bulk bags.
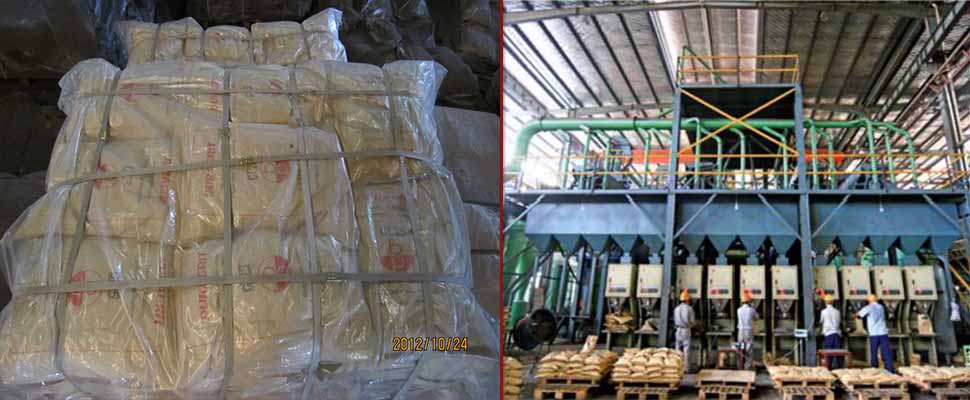
Contact Us
Get in Touch
Blast & Peen Services Pte Ltd
10 Admiralty Street #02-69
North Link Building, Singapore 757695

Fax: +65 6245 8785

www.dura-grit.com
email us now for an obligation free quotation